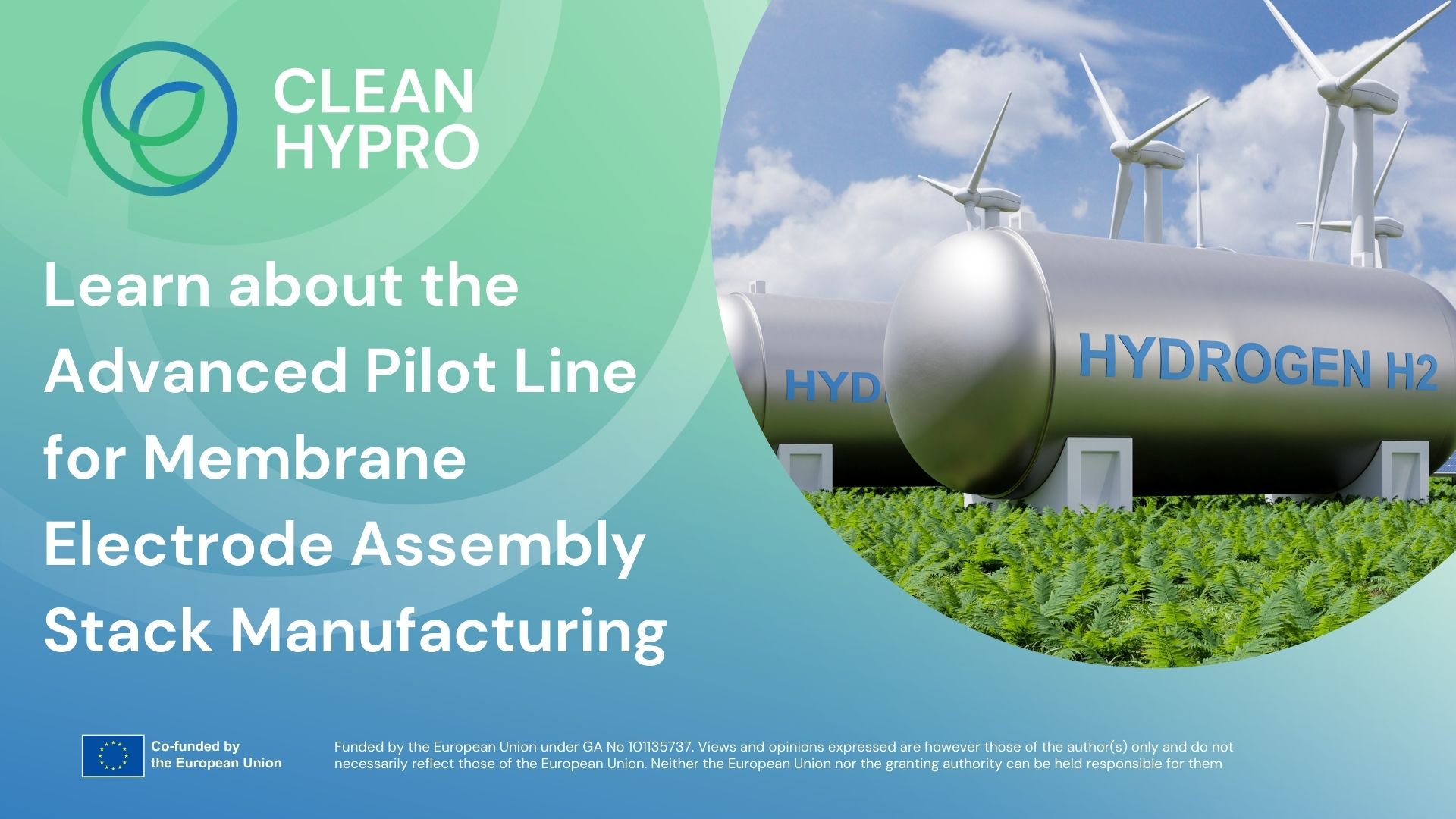
CLEANHYPRO is at the forefront of an initiative aimed at creating a unified access point for industrial partners, particularly SMEs, to expand the production of electrolysis materials and components essential for generating green hydrogen. This effort seeks to decrease production costs and minimize risks, ultimately making green hydrogen more accessible and feasible.
As part of the CLEANHYPRO project, Mondragon Assembly is developing, in collaboration with other partners of the project, a pilot production line for the manufacturing of Membrane Electrode Assembly (MEA) stacks, specifically those incorporating Anion Exchange Membranes (AEM).
Overview of the Pilot Line
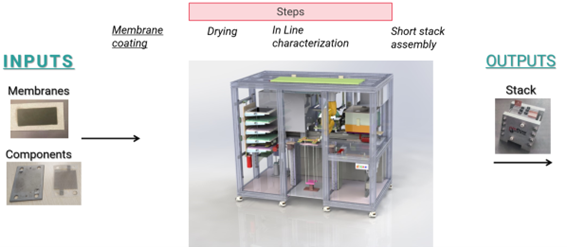
The pilot line Mondragon Assembly has developed focuses on the manufacturing of Membrane Electrode Assembly (MEA) stacks, specifically those incorporating Anion Exchange Membranes (AEM). This advanced manufacturing line automates the assembly of nearly all stack components, including:
- Membranes
- Gas Diffusion Layers (GDL) for both anode and cathode
- Bipolar plates
- Gaskets
- Current distributors
The only exception to this automation is the endplate handling, which are manually integrated.
Key Features and Capabilities
- Robotic Handling: The line utilizes a versatile inverted robot designed to precisely manipulate various components. This ensures accurate placement and assembly, enhancing the overall quality and reliability of the MEA stacks.
- Membrane Coating Processing: A critical step in the manufacturing process involves coating the membranes with a catalyst. This is achieved using ultrasonic spray technology, which guarantees a homogeneous catalyst deposition. The coating process is performed in two stages to cover both sides of the membrane thoroughly.
- Coating Curing:
- IR Curing: After the first catalyst deposition, the membrane undergoes an infrared (IR) curing process with precise temperature control to ensure proper adhesion and performance of the catalyst layer.
- Quality Control:
- Thickness Measurement: Post-curing, the membrane’s thickness is measured in an XY system to verify the uniformity of the coating.
- Visual Inspection: A visual inspection using advanced camera systems follows, identifying any potential defects that may affect the membrane’s functionality.
- Flexibility and Customization:
- Membrane and Stack Sizes: The pilot line is designed to accommodate a range of membrane sizes from 100mm x 100mm to 300mm x 300mm of active area. The line’s dimensions (2.3m x 1.3m) support the assembly of stacks up to 700mm in height and 500kg in weight.
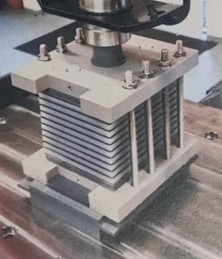
- Recipe Configuration: Within these spatial constraints, the line offers complete flexibility in configuring the manufacturing recipe to meet specific product requirements. This adaptability is crucial for SMEs looking to develop unique and innovative MEA stacks.
The pilot line developed under the Cleanhypro project represents a significant advancement in the manufacturing capabilities available to SMEs in the clean energy sector. With its combination of automation, precision, and flexibility, this pilot line is poised to accelerate the development and production of high-quality MEA stacks, fostering innovation and efficiency in the industry.
Mondragon Assembly is proud to contribute to this transformative project, providing laboratories and SMEs with the tools they need to lead the way in clean energy solutions.