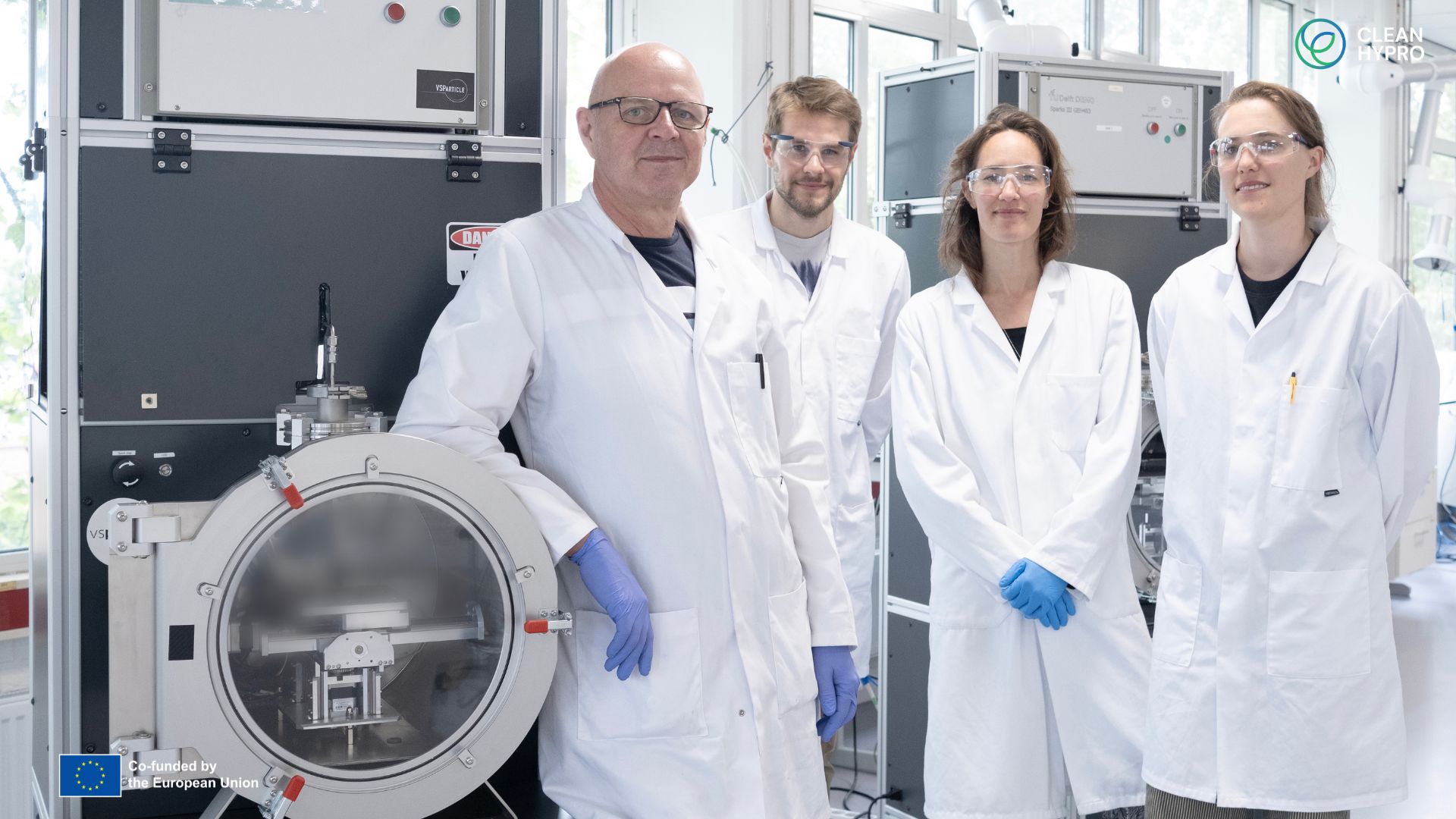
CLEANHYPRO is leading an initiative to create a single entry point for industrial partners, particularly small and medium-sized enterprises (SMEs), to scale up the production of electrolysis materials and components essential for green hydrogen production. This initiative aims at reducing costs and mitigating risks associated with the production process, with the ultimate objective to make green hydrogen more accessible and viable.
Under the CLEANHYPRO project, VSParticle is enhancing its pilot production line to manufacture catalyst layers composed of iridium nanoparticles, a critical component in the electrolyser stack. Concurrently, VSParticle is collaborating with consortium partners to assess the performance of these catalyst layers in an industrial setting, demonstrating their effectiveness and potential for widespread use.
Addressing Iridium Constraints in the Growth of Green Hydrogen
Currently, main obstacles to market adoption of green hydrogen technologies are efficiency of electrolyser and associated costs. Iridium is a key catalyst for green hydrogen production. It has the ability to efficiently split water molecules into hydrogen and oxygen without being consumed in the process, making the electrolysis process more efficient.
However, iridium remains exceptionally rare, with its mining process posing considerable challenges and costs. Globally, only 7-8 mt of iridium is extracted annually for consumption across sectors.[1],[2] With current technologies, ~300-400 kg of iridium is required for each GW of PEM electrolysis capacity. So far, iridium locked in for hydrogen production is quite marginal, as the total installed capacity of PEM electrolysers was only 0.2 GW (2022).[3]
However, hydrogen production is expected to grow massively. International Energy Agency (IEA) estimates that an installed electrolyser capacity of 170-365 GW can be realized by 2030 if all the projects in the pipeline materialized.3 With an assumed market share of 30% for PEM electrolysers, it would require 15 mt – 43 mt of cumulative iridium demand by 2030.
The limited availability of iridium makes it imperative to reduce its usage and recycle as much as possible. Furthermore, iridium can account for about 20-25% of electrolyser stack costs.[4]
Given the scarcity and expense of Iridium, optimizing its use is critical for the sustainability and scalability of green hydrogen production.
VSParticle Nanoprinter Mitigating Iridium Usage
In collaboration with CLEANHYPRO, VSParticle’s catalyst addresses these challenges by enhancing efficiency and reducing material usage, thereby improving performance and cutting costs. VSParticle’s state-of-the-art Nanoprinter technology uses nanoparticle source based on spark ablation technique to generate extremely small particles (2 nm) from bulk rods using electricity and a carrier gas (Figure 1). These iridium nanoparticles serve as catalysts in the electrolyser, offering high efficiency due to their large surface-to-volume ratio, which reduces the amount of iridium needed in the process.
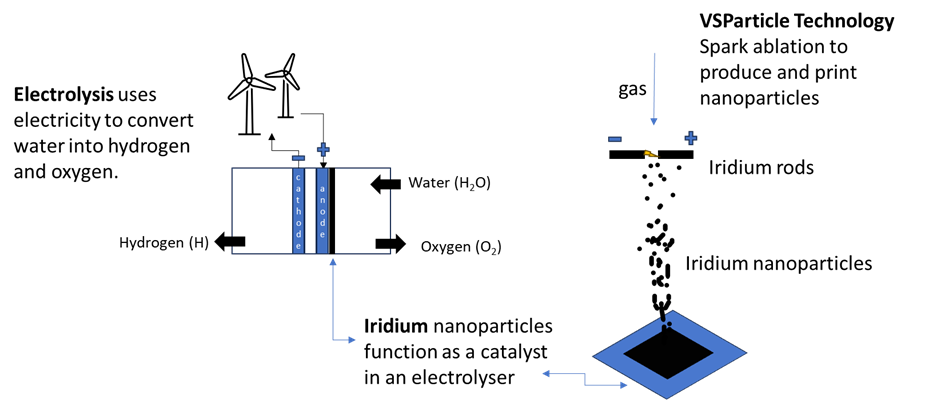
To further its advancement, VSParticle is integrating the next generation of nanoparticle sources in the Nanoprinter to significantly speed up the printing process—a major step towards industrial relevance. The goal is to reduce iridium loading to less than 0.1 mg/cm² while maintaining performance and stability, compared to current loadings in PEM electrolysers of 1 mg/cm², resulting in 10 times less iridium use for hydrogen production.
VSParticle is also optimizing the flow path of nanoparticles within the system to ensure more produced nanoparticles end up on the substrate. Additionally, efforts are underway to collect and recycle all iridium nanoparticles lost in the process, further enhancing the sustainability of the production by reusing 80% of the process gas.
Breakthrough in Nano Printing: Less Iridium Loading and Reduction in Print Time
We have successfully integrated the next generation of nanoparticle source, and our first samples have been printed for characterization (Figure 2).
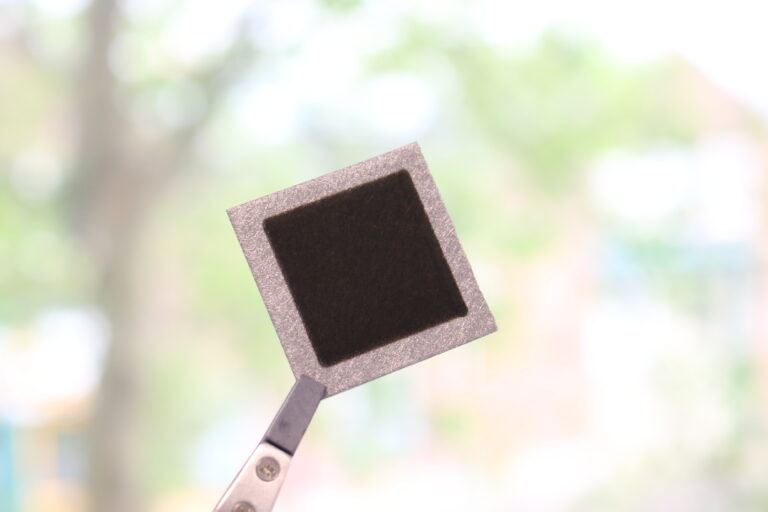
One notable success achieved through this advancement is the reduction in print time to just one minute for a 2.5×2.5 cm² area with a loading of 0.1 mg/cm². This progress represents a significant step towards upscaling the production of nanoparticles to an industrial scale. By upgrading nanoprinting technology, increasing output, reducing losses, and recycling waste, VSParticle aims to minimize costs and risks, thereby accelerating market adoption and scalability.
Unlocking Multi-GW Scale Hydrogen Production
The targets for green hydrogen production are ambitious, with the aim to produce substantial quantities of hydrogen per year and significantly increase the adoption of PEM electrolysers.
VSParticle is committed to further reducing the amount of iridium required and continues its mission to enable researchers to discover novel nanomaterials with unique properties that can solve global challenges. By utilizing nanotechnology for material development, VSParticle aspires to further optimize the use of iridium to unlock multi-GW scale hydrogen production while amplifying research efforts to discover better catalyst materials that do not rely on Earth’s rarest elements.
A Leap Forward in Green Hydrogen Efficiency
VSParticle’s advancements in iridium nanoparticle technology under the CLEANHYPRO initiative mark a significant step towards making green hydrogen production more efficient, cost-effective, and sustainable. By reducing iridium usage while maintaining the catalyst efficiency, and improving recycling processes, VSParticle is paving the way for the broader adoption of green hydrogen technologies. The collaboration with consortium partners and continuous innovation will be crucial in overcoming current challenges and achieving the future targets for hydrogen production.
To learn more about this initiative, watch video on the CleanHyPro Project: 20x Faster Green Hydrogen Production – Powered by VSPARTICLE. For further details about our technology application, visit Catalyst Coated Membranes, CCM (vsparticle.com)
[1] Statista (2023), Supply of Iridium worldwide from 2021 -2023
[2] 240,000 ounces which is converted to metric tons using a division factor of 32,000.
[3] International Energy Agency (2022), Tracking Electrolysers
[4] National Renewable Energy Laboratory (2024) Updated Manufactured Cost Analysis for Proton Exchange Membrane Water Electrolyzers